Polybion’s Origin Story
Polybion isn’t the only bio-based leather brand on the block. Along with Mycoworks and Modern Meadow, Polybion is one of the original names in bio-based leather production. The concept of SCOBY-derived bioleather was popularized by Suzanne Lee’s BioCouture project, which she spoke about in her seminal 2011 TED Talk.
Polybion was founded in 2015 by brothers Axel and Alexis Gómez-Ortigoza and Bárbara González Rolón, PhD, shortly after Axel’s participation in the 2013 synthetic biology competition iGEM. As of today, May 7th 2024, Celium™ is available for global distribution.
I connected with Alexis Gómez-Ortigoza, Co-Founder and CFO, to learn Polybion’s origin story. The brothers’ enthusiasm for commercializing Axel’s innovation was inspired by their father’s journey as a successful tech entrepreneur and influenced by their mother’s work as a chemist. Gómez-Ortigoza remarks “We grew up having dinner conversations about tech and business trends. My mom ran her own chemistry lab for the medical industry for years. When we were small, we’d play in the lab. We’ve always been exposed to nature, technology, and laboratories.”
Aided by material scientist Dr. González Rolón, the team applied for and received a government grant in Mexico to start pilot production.
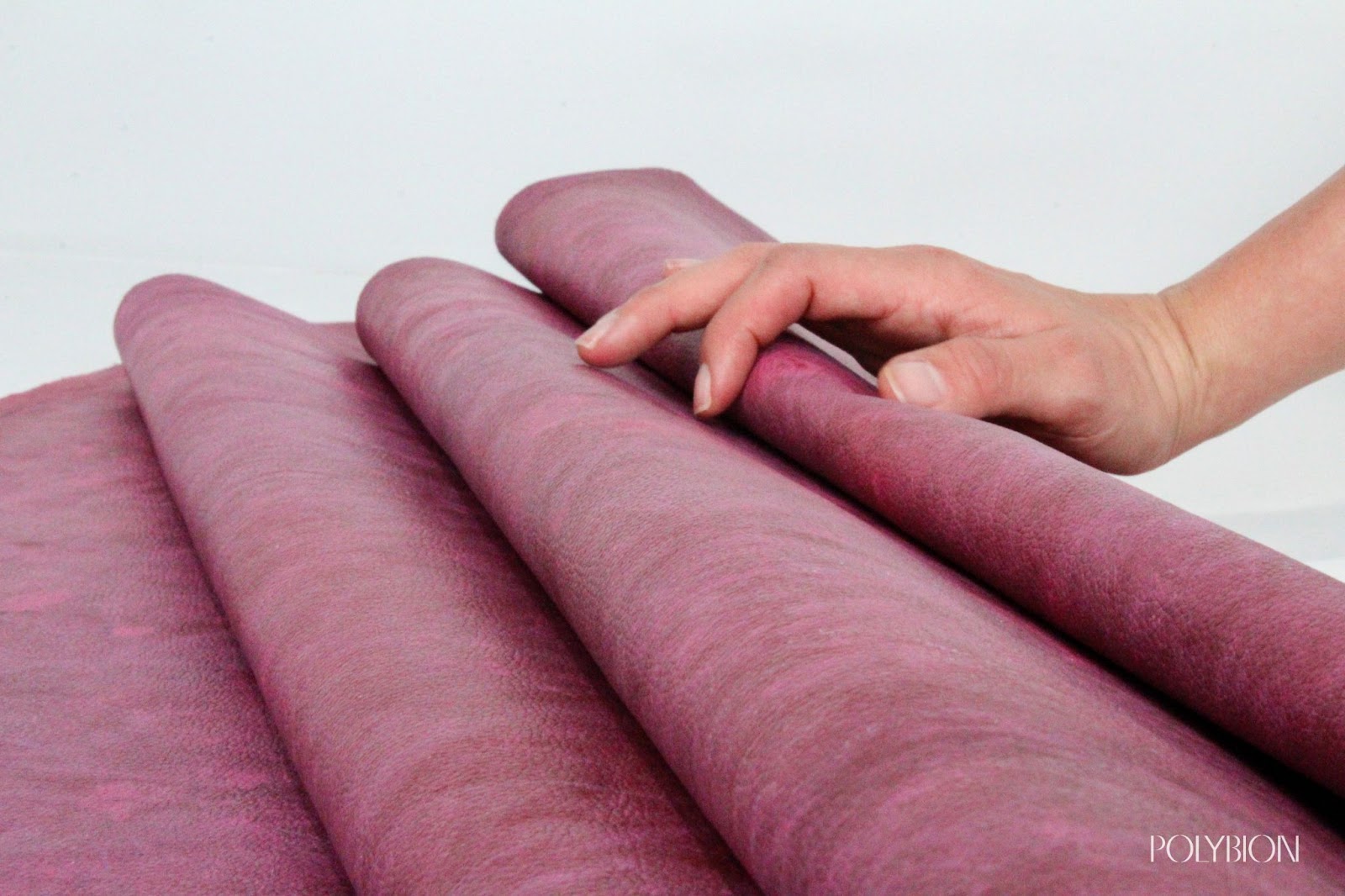
The Science of Celium™
While early R&D at Polybion leveraged mycelium (composed of chitin) to create bio-based leather, the current process is focused on nanocellulose production by genetically-engineered bacteria. Cellulose, the most abundant polymer on Earth, is a structural molecule composed of the sugar glucose, and is responsible for the structural integrity of trees and other plants.
Polybion’s process to produce Celium starts by cultivating a SCOBY in a large-scale vertical fermentation vessel. Once it’s grown to the right thickness, it’s cured in a chromium-free tanning process, then dyed and finished as needed. SCOBY stands for a “Synbiotic Community of Bacteria and Yeast” and is the mother culture for the production of kombucha. The SCOBY creates a slippery cellulose pancake, known as a pellicle, which floats atop the liquid and is harvested for tanning.
Chromium, used in most traditional animal leather tanning, is extremely harmful to both the environment and to humans. If inhaled during processing it can cause cancer. Chromium can also be absorbed through the skin when wearing a chromium-tanned garment. The fact that Polybion opts for Chromium-free tanning agents is an important detail.
Polybion has an in-house R&D team of five scientists committed to using genetic research to improve the efficiency of bacterial nanocellulose production in industrial conditions. Through genetic engineering, they’re optimizing the bacteria for nanocellulose production and reducing the time needed to grow a SCOBY to the desired thickness. Over the past two years of R&D, they’ve been able to reduce the growth time by 62%.
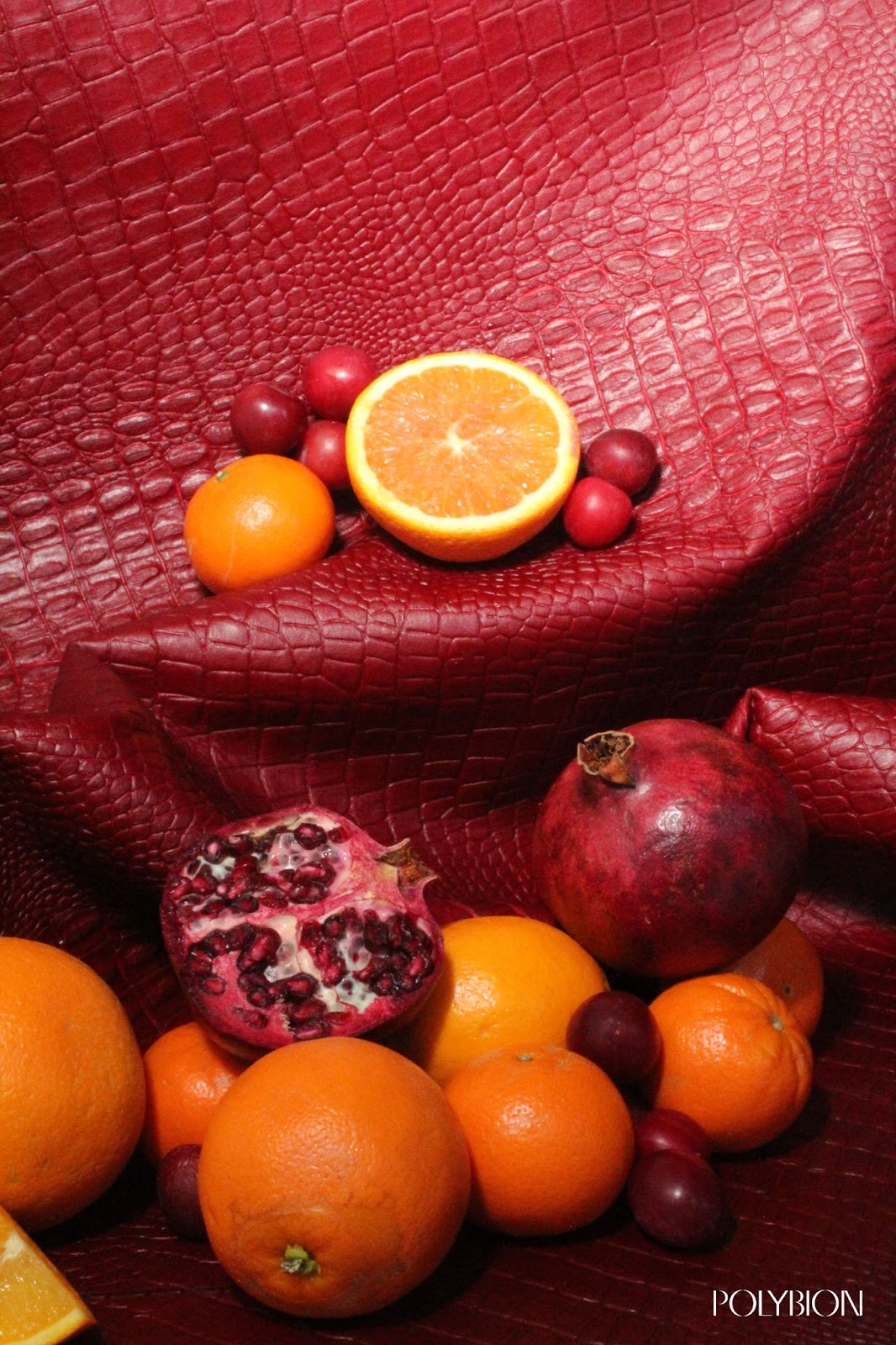
If you’ve read our piece on the Tômtex M-series Mushroom Leather handbag, you’ll remember that chitin is another naturally-occurring structural compound. Chitin, found in the cell walls of fungi, is also found in composite with calcium carbonate in the exoskeletons of crustaceans and insects. Chitin and cellulose have unique attributes, both responsible for structural integrity.
Polybion opted to switch from a mycelium-based process to a bacteria-based process because they prefer the ease of working with prokaryotic cells over eukaryotic cells. Genetic modification, along with scaling fermentations, are much easier for them in a liquid medium. Additionally, the Polybion team enjoys the increased strength that working with bacteria provides. Gómez-Ortigoza reported a 100 fold increase in resolution of the material as compared with their earlier mycelium prototypes, attributed to the smaller cell size of bacteria.
Sustainability: Local Supply Chains, Food Waste, & Solar Power
Polybion takes advantage of the opportunity present in creating a radically different product to craft their entire supply chain from scratch. Without having ties to legacy suppliers or antiquated systems, Polybion keeps its supply chain as tight as possible. Gómez-Ortigoza shared: “we do everything in-house, from food waste processing for feedstock to the tanning of the bioleather. Owning every step of the process is one of our keys to success.” Polybion has even been able to source local manufacturing equipment from their industrial region of Irapuato, Mexico.
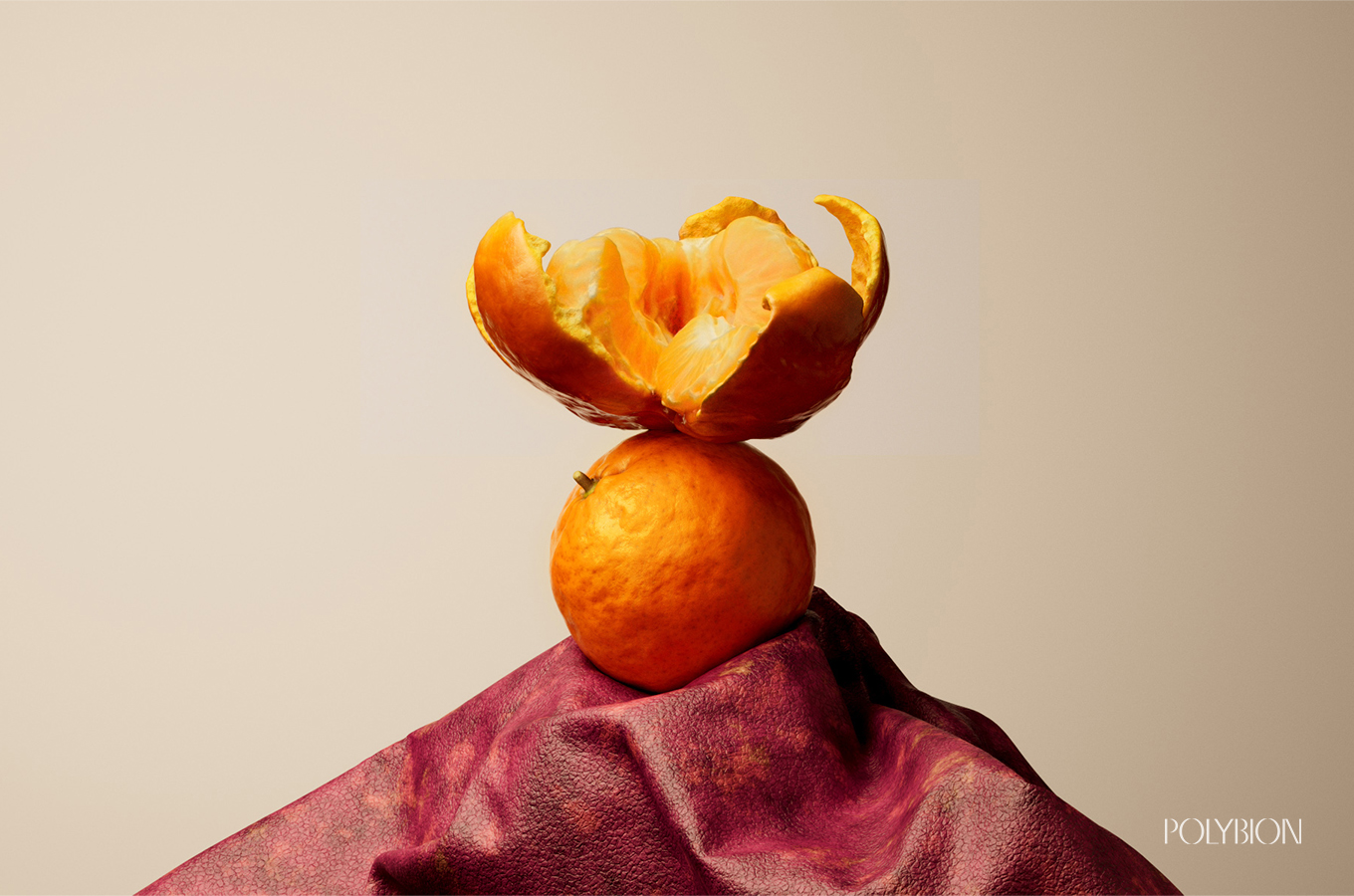
This contrasts sharply with the supply chains for most materials. Take a plant fiber, cotton, as an example. Raw materials may be farmed halfway across the world from the processing plant that spins the fiber into a usable thread. That thread may travel back across the globe to be woven into textiles before it’s ready to be sent to cut-and-sew to be made into a garment.
In modern animal leather production the ranching, slaughtering, and tanning rarely occur in the same country, much less in the same facility. So it is exceptional for Celium to be grown, processed, dyed, and finished all under one roof. Furthermore, the Polybion team capitalizes on the fact that they’re surrounded by fruit packaging companies in Irapuato, Mexico, to divert fruit waste which provides 90% of their feedstock.
Polybion strives for circularity where feasible, including the re-use of tanning liquids. The process is much faster than with cowhide and the tanning agents stay fresh and are able to be used on future batches. In regards to energy use, Polybion has its own solar panel array and provides much of its own energy demand.
A preliminary LCA (pLCA) performed by ETH Zurich MSc student Simone Bründl, revealed that Celium production consumes 97% less water and depletes 95% less fossil fuels than does traditional cow leather tanning.
For products made primarily out of leather, Sustainability metrics like this really make a difference. Ganni A/S, a Danish fashion brand with a growing reputation for innovation took notice.
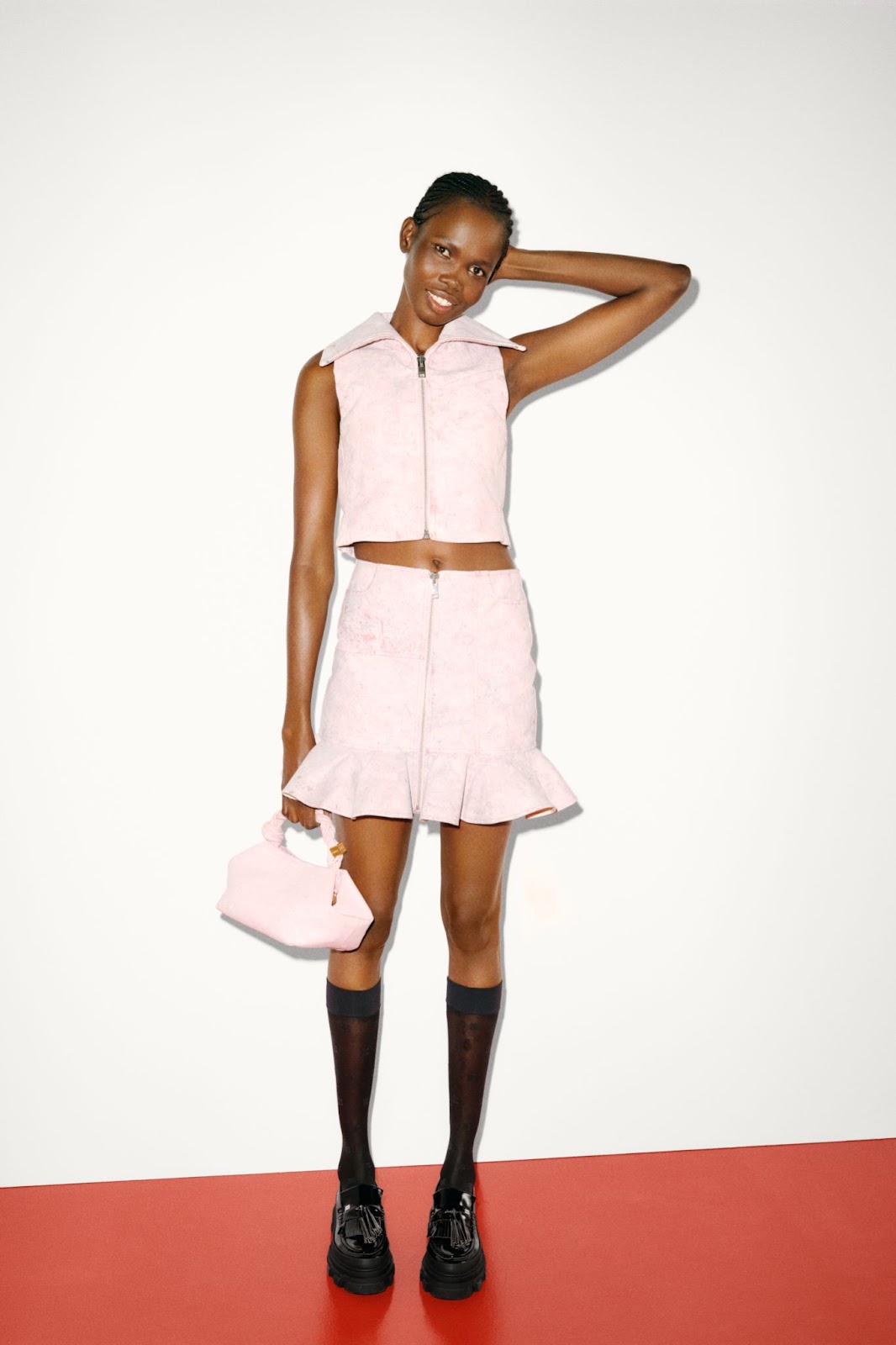
Ganni, a Forerunner in Sustainable Materials Adoption
In the material innovation world, it’s not uncommon for collaborations to end after a prototype and a press release, rarely progressing past the capsule stage.
Ganni stands out as a brand that understands the real potential of using and scaling new materials. Julie Verdich, Material Innovation Lead for Ganni, reached out to Alexis of Polybion via LinkedIn message back in 2022. They met in Ganni’s Paris office. Relaying the story, Gómez-Ortigoza remarked with a smile “by the time our plane landed in Mexico from Europe, we had a proposal in our inbox from Ganni.” In January 2023, Polybion shipped production samples of Celium to Ganni’s office in Copenhagen. By July 2023, the first prototype for their collaboration, a jacket, debuted at the Global Fashion Summit. By the Biofabricate Summit in January 2024, the teams showcased prototypes of the Bou Bag in Celium as well as the Signature Blazer in Celium.
Gómez-Ortigoza speaks on the rapid timeline of prototype creation by the Ganni team: “This speaks volumes about the speed at which the Ganni team iterates. They are willing to take risks and make bold actions. From day one, Ganni totally embraced the fact that our material was a new thing.” Ganni’s willingness to embrace the unique aspects of Celium, rather than try to fit Celium into their existing processes, is what sets them apart as a fashion brand that takes its materials transition seriously.
As a materials innovation scouting potential brand partnerships, Gómez-Ortigoza says to “look for brands who are truly dedicated to sustainability, who significantly invest in the success of their partnerships through human and financial capital.” He also mentioned that the Ganni team provides rapid and thorough feedback throughout their process, helping them Polybion improve their product through each step of the partnership.
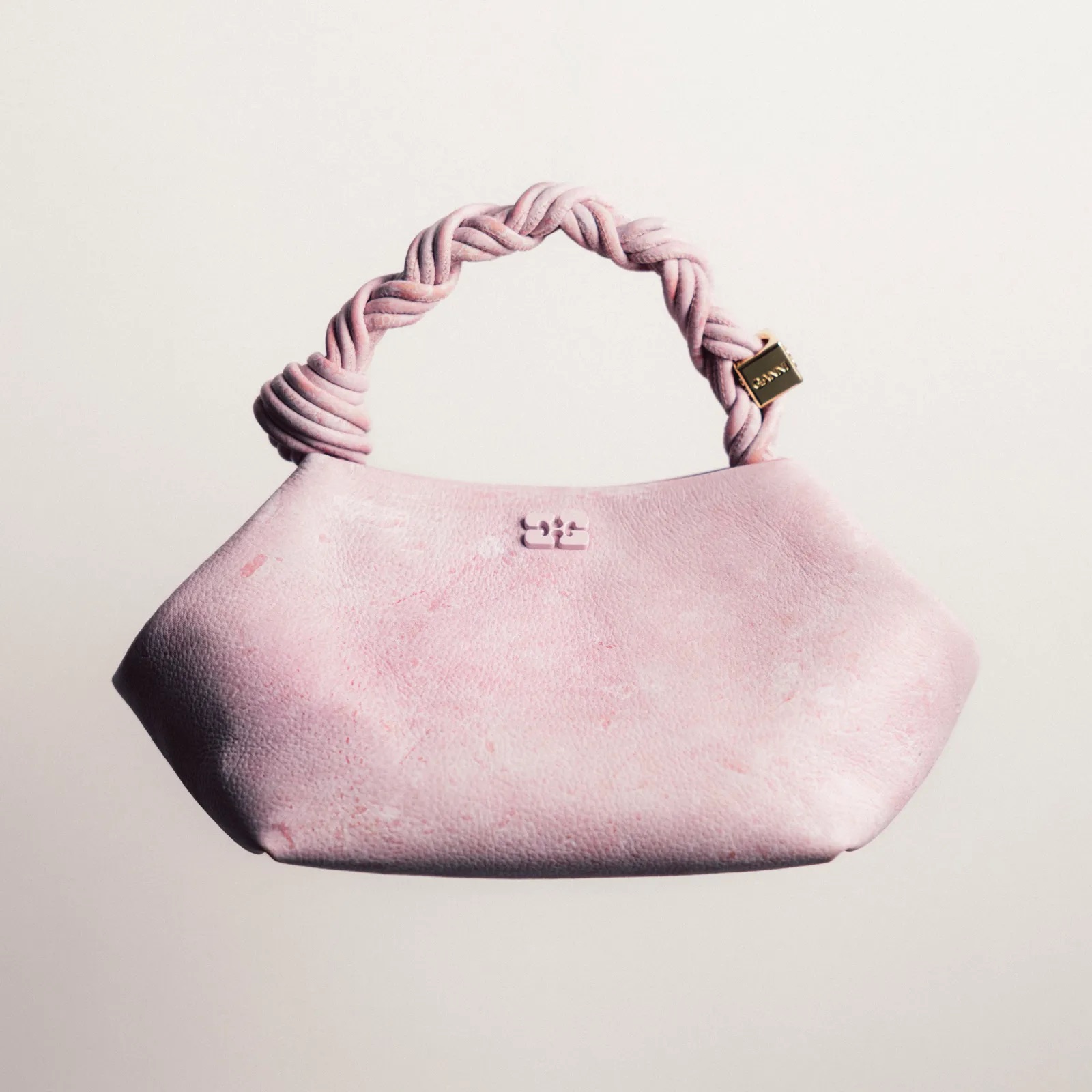
What’s next for Polybion?
Polybion and Ganni plan a wider release in the next 12 months. As Polybion launches their material globally, they are seeking brands ready to collaborate and scale together.
What materials do you want to see adopted by fashion brands?
Ganni has previously sourced alternatives such as Vegea, Ohoskin, Oleatex, Natural Fiber Welding’s Mirum. Ganni was also an early adopter of Mylo, the mycelium leather made by Bolt Threads that ceased production in 2023. “We’re testing as many [materials] as we can and helping them to get to market because ultimately that’s to our benefit,” Ganni founder Nicolaj Reffstrup explains. “Obviously launching products that turn out to never scale hurts too, but that’s something we learn from.”
Ganni has also iterated on their iconic Bou Bag with Modern Synthesis and is known for other collaborations, such as with the fur alternative BioFluff. We’re now in the era of real commercial adoption of biomaterials. What collaborations do you want to see next?
We hope that you’ll find Polybion x Ganni to be a refreshing example of fruitful partnership. 🍉 Celium is available for worldwide purchase as of May 7th 2024.